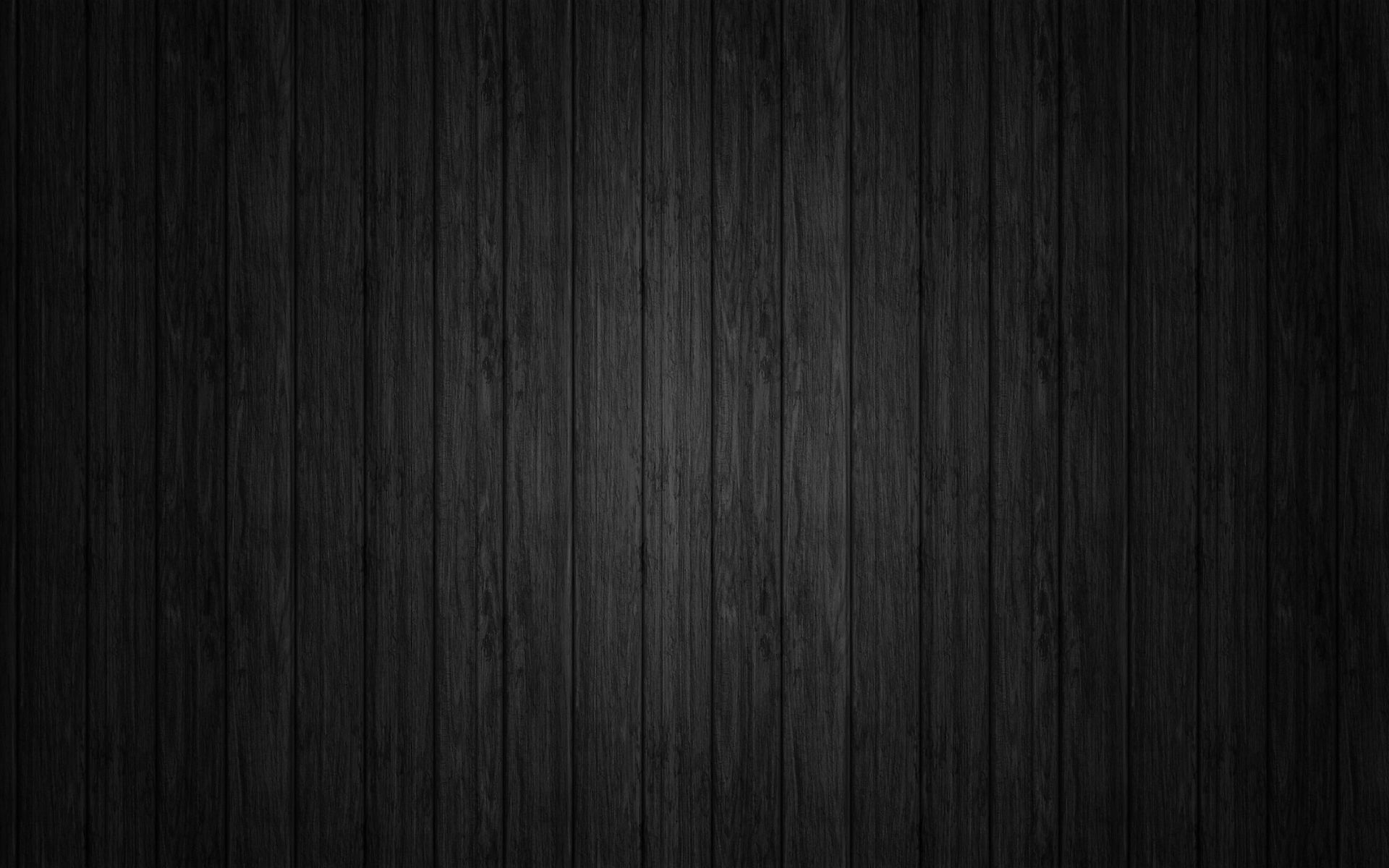

IV Packing Line
COMPLETE IV PACKING LINE

LEAK TEST MACHINE
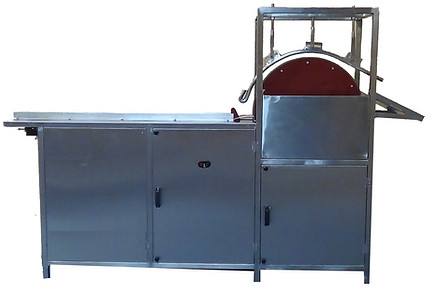
Salient Features:
-
Structure made of SS 304 rigid construction.
-
Special Nylon rubber endless belt is used for the conveyor for long life & durability.
-
Specially designed SS 304 hood for internal lighting with black & white stations.
-
Guide provision for transfer of bottles into initial 2 tracks & final 3rd track for conveying the tested products.
-
Easy & comfortable visualization position for operators for inspection.
-
Specially designed hard chrome roller with self-aligned bearings for longer life of conveyor.
-
Sitting stools arrangement for 8 persons (OPTIONAL).
-
Bowl for the dust cap at both side of the conveyor.
-
Partition after every two booth.
-
Tension mechanism is provided for adjusting the belt tension.
-
AC variable drive for variable speed as per product size. The drive is fitted in the control panel below the conveyor.
-
Usage of reliable & proven components such as Bonfiglioli/Motovario/Rotomotive/Gennext Motor, Delta make AC variable drive etc.
Operation:
-
Bottles coming from onward machine/to be loaded manually to the conveyor.
-
The bottles are automatically bifurcated into 2 adjoining tracks with the help of guide.
-
The operators pick up the bottles from the 2 side tracks. They visually inspect the bottles with the help of black and white booth with tube light on conveyor for any breakage, leakage, proper volume filled & sealed and any strange particles in filled bottle.
-
After inspection the bottles are placed in the central track, which is transfer for further operation.
ONLINE VISUAL INSPECTION CONVEYOR

Salient Features:
-
Structure made of SS 304 rigid construction.
-
Special Nylon rubber endless belt is used for the conveyor for long life & durability.
-
Specially designed SS 304 hood for internal lighting with black & white stations.
-
Guide provision for transfer of bottles into initial 2 tracks & final 3rd track for conveying the tested products.
-
Easy & comfortable visualization position for operators for inspection.
-
Specially designed hard chrome roller with self-aligned bearings for longer life of conveyor.
-
Sitting stools arrangement for 8 persons (OPTIONAL).
-
Bowl for the dust cap at both side of the conveyor.
-
Partition after every two booth.
-
Tension mechanism is provided for adjusting the belt tension.
-
AC variable drive for variable speed as per product size. The drive is fitted in the control panel below the conveyor.
-
Usage of reliable & proven components such as Bonfiglioli/Motovario/Rotomotive/Gennext Motor, Delta make AC variable drive etc.
Operation:
-
Bottles coming from onward machine/to be loaded manually to the conveyor.
-
The bottles are automatically bifurcated into 2 adjoining tracks with the help of guide.
-
The operators pick up the bottles from the 2 side tracks. They visually inspect the bottles with the help of black and white booth with tube light on conveyor for any breakage, leakage, proper volume filled & sealed and any strange particles in filled bottle.
-
After inspection the bottles are placed in the central track, which is transfer for further operation.
AUTOMATIC HORIZONTAL (TOP) STICKER LABELING MACHINE
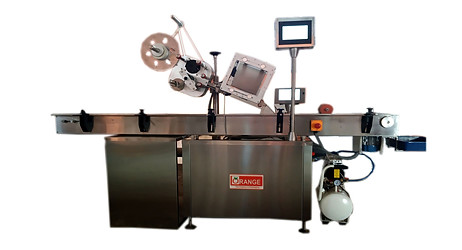
Machine Description:
-
The unit is made Compact & Versatile as per GMP norms.
-
Applicator controlled by PLC and Operated with HMI.
-
Various label Height position adjustment with help of S.S sliding pipe assembly.
-
Imported sensor makes Leuze/Sick.
-
All automation parts like VFD, HMI and PLC system CE certified and Imported.
-
Specially design dispenser for Accurate label Dispensing.
-
All moving parts cover by safety guard.
-
User friendly & very less maintenance.
-
Specialized Belt conveyor for product transmission.
-
Specialized Imported sensor for accurate Pouch sensing.
-
Special Material sponge for uniform label pressing.
-
All M.S exposed parts will be covered with S.S cover or Powder coated.
-
Heavy and Rigid Structure and Machine with Matt Finished.
Component Description:
-
VFD DRIVES- MITSUBISHI
-
PLC- MITSUBISHI
-
HMI- MITSUBISHI
-
SENSOR SET- SICK MADE IN GERMANY
-
MOTOR GEAR BOX- ROTOMOTIVE
Advance Features:
-
Touch Screen operated HMI CE Certified.
-
Special functions like Product Delay, Label Length, label speed and Multiple Program facility for easy and fast operation.
-
Bottles/Minute and Total count facility for Output Records.
-
Password Protection on customer request.
-
Easy to use adjustments, requiring a minimum tools or change of parts.
AUTOMATIC HORIZONTAL FLOW WRAPPING MACHINE
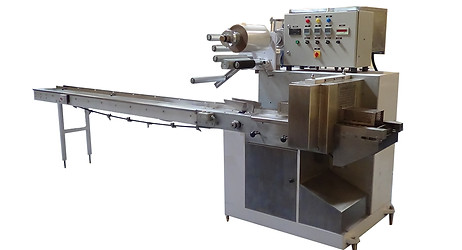
Salient Features:
-
The machine is manufactured or developed accordance with GMP standards.
-
Rigid vibration free construction,noiselessfor trouble free performance.
-
The structure is made of MS and cladded with SS 304.
-
The contact parts are made of SS 304.
-
All the Bearings are makes of SKF OR NTN.
-
Cross sealing heaters operate on 220 volt.
-
Specially designed jaw mechanism.
-
Conveyor made of specialized positive pusher on chain. In-feed conveyor 2 meter long for easy feed of our product.
-
MAIN ON/OFF SWITCH: This is a switch to switch ON/OFF power to the machine.
-
EMERGENCY SWITCH: This is a push button to stop the machine immediately.
-
All Electrical Components are ISI Marks.
-
Gear & sockets EN-8.
-
Tower light.
-
The construction of machine‘s electrical panel is in line with the IP 55 standard.
Operation:
-
Bottles to be loaded in horizontal position manually on the flow wrapping chain conveyor.
-
After that bottles will run on positive pusher feeding conveyor with uniform distance between the two bottles.
-
The speed of the conveyor is adjusted (synchronized) to maintain the desired speed with the help of variable drive.
-
The BOPP roll is fitted on the roll disc & is guided by the guide rolls.
-
The machine is operated with the help of switches.
Complete machine can be divided in following sub sections:
-
Machine Body & Components
-
BOPP film feeding system
-
Centre Sealing System
-
Horizontal Sealing & Cutting System
PACKING CONVEYOR

Salient Features:
-
Structure is made of SS 304 rigid construction.
-
Desired Length can be provided as per customer requirement.
-
SS elegantly matt finishing.
-
Adjustable height of conveyor belt, to align with other machine of the line.
-
Specially designed hard chrome roller with self-aligned bearings for longer life of conveyor.
-
Tension mechanism is provided for adjusting the belt tension.
-
AC variable drive for variable speed as per product size. The drive is fitted in the control panel below the conveyor.
-
Stopper arrangement at the end of conveyor for preventing falling/breakage of bottles.
-
Working space of 6, 9 & 12 inches on each side of the conveyor as per customer requirement.
-
Can be supplied with Castor wheels (OPTIONAL).
-
Usage of reliable & proven components such as Bonfiglioli/Motovario/Rotomotive Motor, Delta make AC variable drive etc.
Operation:
-
The conveyor transmits the products from the labeling machine, and brings till the end of conveyor for further process of packing.
-
During these process, the operators picks up the products & does necessary action like primary packing, secondary packing.
BOPP CARTON BOX TAP SEALING MACHINE

Technical:
Power Supply: 230 V AC / 50 Hz / Single Phase
Power Consumption: 660 Watt
Control System: Electrical Switchgear
Carton Size: L 120 mm Unlimited X W 120 mm To 450 mm X H 120 mm To 450 mm
Table Height: 750 mm
Speed: Up to 20 Box/Minute
Weight: 220 kg Approx.
​
Parts:
Body: Sheet Metal Steel Construction With Powder Coating
Mechanics: Made From MS Solid Material
Conveyor: MS Roller, Nylon Sandwich Belt
​
Features:
Easy To Operate
Easy Movable
Low Maintenance